Air Compressor keaser 135KW Heavy Duty Monster Machine. this is highly advance computerised programmed Compressor made by Germany it's creates high pressure maximum 10bar into a 2000ltr Air receiver tank within a second. A rotary-screw compressor is a type of gas compressor, such as an air compressor, that uses a rotary-type positive-displacement mechanism. These compressors are common in industrial applications and replace more traditional piston compressors where larger volumes of compressed gas are needed, e.g. for large refrigeration cycles such as chillers, or for compressed air systems to operate air-driven tools such as jackhammers and impact wrenches. For smaller rotor sizes the inherent leakage in the rotors becomes much more significant, leading to this type of mechanism being less suitable for smaller compressors than piston compressors.
The screw compressor is identical to the screw pump except that the pockets of trapped material get progressively smaller along the screw, thus compressing the material held within the pockets. Thus the screw of a screw compressor is asymmetrical along its length, while a screw pump is symmetrical all the way.
The gas compression process of a rotary screw is a continuous sweeping motion, so there is very little pulsation or surging of flow, as occurs with piston compressors. This also allows screw compressors to be significantly quieter and produce much less vibration than piston compressors, even at large sizes, and produces some benefits in efficiency.
working - Rotary-screw compressors use two very closely meshing helical screws, known as rotors, to compress the gas. In a dry-running rotary-screw compressor, timing gears ensure that the male and female rotors maintain precise alignment without contact which would produce rapid wear. In an oil-flooded rotary-screw compressor, lubricating oil bridges the space between the rotors, both providing a hydraulic seal and transferring mechanical energy between the rotors, allowing one rotor to be entirely driven by the other. Gas enters at the suction side and moves through the threads as the screws rotate. The meshing rotors force the gas through the compressor, and the gas exits at the end of the screws. The working area is the inter-lobe volume between the male and female rotors. It is larger at the intake end, and decreases along the length of the rotors until the exhaust port. This change in volume is the compression. The intake charge is drawn in at the end of the rotors in the large clearance between the male and female lobes. At the intake end the male lobe is much smaller than its female counterpart, but the relative sizes reverse proportions along the lengths of both rotors (the male becomes larger and the female smaller) until (tangential to the discharge port) the clearance space between each pair of lobes is much smaller. This reduction in volume causes compression of the charge before being presented to the output manifold.The effectiveness of this mechanism is dependent on precisely fitting clearances between the helical rotors and between the rotors and the chamber for sealing of the compression cavities. However, some leakage is inevitable, and high rotational speeds must be used to minimize the ratio of leakage flow rate over effective flow rate.
In contrast to Roots blowers, modern screw compressors are made with different profiles on the two rotors: the male rotor has convex lobes which mesh with the concave cavities of the female rotor. Usually the male rotor has fewer lobes than the female rotor, so that it rotates faster. Originally, screw compressors were made with symmetrical rotor cavity profiles, but modern versions use asymmetrical rotors, with the exact rotor designs being the subject of patents.
#mechanical #technology #youtubeshorts #house #youtuber #youtubechannel #youtubevideo #trending #youtubeindia #viralvideo #electricalengineering #manufacturer #computer #programming #reels #reelsinstagram #reelsvideo #viralvideo #viralshorts #viral #mechanicalengineering #factory #fact #search #subscribers #youtubeseo #like #channel #india #industry #revolution #manufacturing #trending
The screw compressor is identical to the screw pump except that the pockets of trapped material get progressively smaller along the screw, thus compressing the material held within the pockets. Thus the screw of a screw compressor is asymmetrical along its length, while a screw pump is symmetrical all the way.
The gas compression process of a rotary screw is a continuous sweeping motion, so there is very little pulsation or surging of flow, as occurs with piston compressors. This also allows screw compressors to be significantly quieter and produce much less vibration than piston compressors, even at large sizes, and produces some benefits in efficiency.
working - Rotary-screw compressors use two very closely meshing helical screws, known as rotors, to compress the gas. In a dry-running rotary-screw compressor, timing gears ensure that the male and female rotors maintain precise alignment without contact which would produce rapid wear. In an oil-flooded rotary-screw compressor, lubricating oil bridges the space between the rotors, both providing a hydraulic seal and transferring mechanical energy between the rotors, allowing one rotor to be entirely driven by the other. Gas enters at the suction side and moves through the threads as the screws rotate. The meshing rotors force the gas through the compressor, and the gas exits at the end of the screws. The working area is the inter-lobe volume between the male and female rotors. It is larger at the intake end, and decreases along the length of the rotors until the exhaust port. This change in volume is the compression. The intake charge is drawn in at the end of the rotors in the large clearance between the male and female lobes. At the intake end the male lobe is much smaller than its female counterpart, but the relative sizes reverse proportions along the lengths of both rotors (the male becomes larger and the female smaller) until (tangential to the discharge port) the clearance space between each pair of lobes is much smaller. This reduction in volume causes compression of the charge before being presented to the output manifold.The effectiveness of this mechanism is dependent on precisely fitting clearances between the helical rotors and between the rotors and the chamber for sealing of the compression cavities. However, some leakage is inevitable, and high rotational speeds must be used to minimize the ratio of leakage flow rate over effective flow rate.
In contrast to Roots blowers, modern screw compressors are made with different profiles on the two rotors: the male rotor has convex lobes which mesh with the concave cavities of the female rotor. Usually the male rotor has fewer lobes than the female rotor, so that it rotates faster. Originally, screw compressors were made with symmetrical rotor cavity profiles, but modern versions use asymmetrical rotors, with the exact rotor designs being the subject of patents.
#mechanical #technology #youtubeshorts #house #youtuber #youtubechannel #youtubevideo #trending #youtubeindia #viralvideo #electricalengineering #manufacturer #computer #programming #reels #reelsinstagram #reelsvideo #viralvideo #viralshorts #viral #mechanicalengineering #factory #fact #search #subscribers #youtubeseo #like #channel #india #industry #revolution #manufacturing #trending
- Категория
- чиллеры
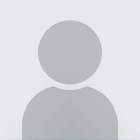
Комментариев нет.